General use synthetic rubbers
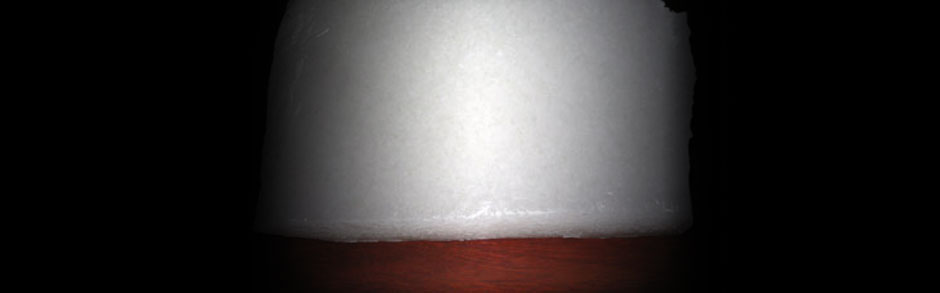
Lorem ipsum dolor sit amet, consectetur adipisicing elit. Eveniet et tempore accusamus earum, suscipit veritatis quisquam dolor obcaecati, enim velit?
Thanks to IR it was possible to get by combination an equivalent material to the natural rubber, and its formulation is quite similar to the NR one. In moulding operations, by compression as well as by injection, these synthetic polyisoprenes flow much easier than natural rubber, what can be particularly more profitable when moulding by injection or in the manufacture of difficult or short thickness and large surface parts; on the other hand, its lower tear strength, mainly subjected to vulcanization temperatures, can make these complex parts difficult to be mould released.
In the extrusion, calendaring and preparation of combined articles, the synthetic polyisoprenes do not show special problems, except those that could come from its lower toughness and resistance being raw, and, in the particular case of those obtained with butyl lithium, those which come from its cold flow. The synthetic polyisoprenes lowest trend to crystallize become into lower values of hardness, rigidity, tensile and tear strength, and by a lower rate of retention of these compounds without loads.
The higher purity of the synthetic polyisoprenes offers a better performance as electrical insulator. As these are synthetic materials, they show a uniformity of characteristics which become unattainable for natural rubber.
Butadiene-Estyrene Rubbers (SBR)
Butadiene-Styrene Rubbers make the highest volume type of synthetic rubber consumption. As the natural rubber, the SBR can vulcanize by means of sulphur and accelerators, by means of peroxides or by means of other special vulcanizing agents.
SBR is not as sensitive to rust as natural rubber because, apart of its intrinsic nature, it counts with an antioxidant per se. Besides, SBR rubbers need the presence of reinforcement loads to reach a satisfactory level of mechanical strength. An abrasion strength is obtained with such loads which often exceeds the natural rubber one.
SBR rubbers are clearly inferior to natural rubbers in relation to resilience. Concerning the performance facing the dynamic fatigue, SBR are better than natural rubber because cracks take more time to appear in them, but, once these last ones start appearing, due to fatigue, or due to an unusual mechanical laceration, they spread quicker than in vulcanized natural rubbers.
Concerning their main uses, the manufacture of covers for tyres, cables insulation, moulded technical articles, shoes, belts, hoses, or adhesives point out among some others.
Polybutadiene polymers are among the first synthetic rubbers manufactured on an industrial scale. When it they are used as an only rubber during a vulcanizing process, the BR of a high content of cis-1,4 give tensile and tear strength, and elongation at break higher values. Their abrasion strength is also better, which is higher in all BR than in SBR and natural rubbers.
The high resilience of the vulcanized products of BR is one of its special characteristics, which is much higher than the natural rubber one at room temperature. Its cold resistance is also outstanding. BR of high cis content keep their high resilience to temperatures as low as -40º C.
If natural rubber is progressively replaced by BR in a formulation until the proportion of this last one does not exceed a value of approximately 40-45 per cent, it does not turn into a perceptible worsening of the production characteristics, but also the following advantages are obtained instead:
- Better abrasion resistance
- Less tendency to fatigue cracking
- Higher reversion strength
In the same way, in the case of a SBR formulation, until approximately 50% of it is not replaced by BR, the production characteristics does not turn affected in a sensitive way, and instead of that we get:
- Better abrasion resistance
- Less tendency to fatigue cracking
- Higher resilience and less hysteresis, what means a lower heat generation, and lower running temperatures therefore